——激光雷达+AI视觉融合方案破解矿山卡机停机难题
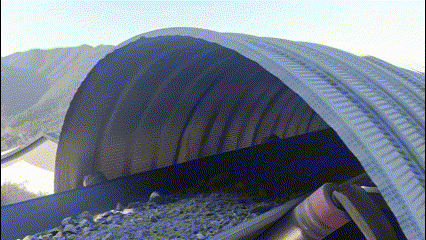
客户背景:水泥矿石的粉碎工序痛点
客户作为国内领先的水泥生产企业,目前年平均台产在4346吨,月平均台产为20万吨,其矿山生产线采用“开采-粉碎-研磨”一体化流程。在粉碎工序中,矿石需经破碎机处理后通过传送带进入研磨环节,但长期面临两大核心挑战:
- 隐形设备损耗:破碎机刀片磨损或故障时,未粉碎的大块矿石(>80mm)进入下游,导致研磨卡机,单次停机损失超50万元;
- 人工巡检滞后:传统人工抽检每2小时一次,无法实时监测矿石粒度,异常发现平均延迟47分钟。
杉维科技矿石粒度检测方案:激光雷达+AI视觉实时粒度管控
针对客户的产线特性,杉维科技部署 「矿石粒度智能监测系统」 ,构建三级防御体系:
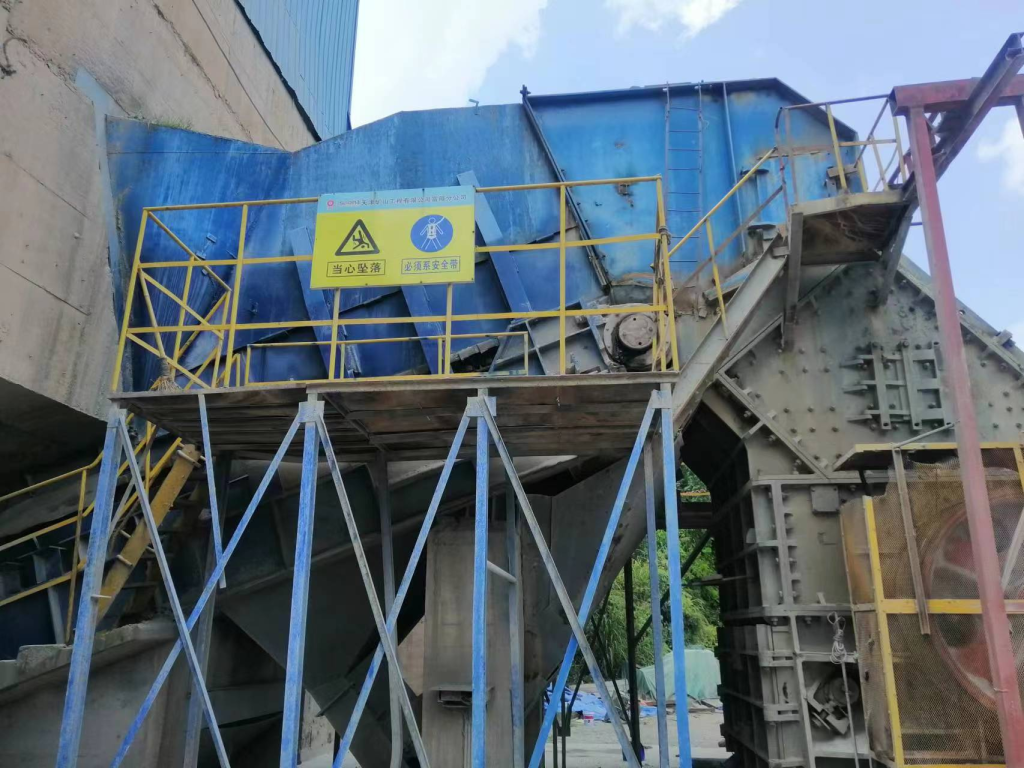
1. 粉碎机健康预警
- 毫米波激光扫描:Vi-100激光雷达(100Hz)实时扫描传送带矿石表面,检测精度达±3mm;
- 刀片磨损预判:AI算法分析粒度分布变化,当P80值波动>5%时自动预警,提示刀具检修;
- 动态参数调节:联动破碎机PLC系统,遇大块矿石(>设定阈值)自动调整破碎压力。
2. 研磨工序前哨检测
- 200fps高速抓拍:CM-200工业相机捕捉传送带全幅图像,60ms内完成异物识别;
- 多级粒度拦截:设置研磨准入粒度阈值(如<50mm),超标矿石触发气动分拣装置;
- 3D点云建模:重建矿石三维轮廓,精准计算等效投影直径,误判率<0.8%。

3. 全链路数据贯通
- 边缘计算决策:RP-8边缘计算盒(30TOPS算力)实时处理数据,延迟<200ms;
- 数字孪生监控:中控大屏同步显示粒度分布热力图、设备健康指数、产能预测曲线;
- 预防性维护:基于历史数据生成刀片更换周期建议,设备故障率降低67%。
实施成效:从“救火式维修”到“预测性管控”
系统上线后,水泥生产实现粉碎工序革命性升级:
- 粉碎机维护成本降低30%,减少刀片磨损导致的故障停机。
- 生产效率提高25%,确保矿石粒度符合标准,减少下游堵塞。
- 人工巡检工作量减少90%,远程监测替代人工检测,提高智能化水平。
“杉维的系统就像给生产线装上了‘CT扫描仪’,现在不仅能实时看到矿石‘内脏’,还能预判设备‘生病’。这套方案让我们的运维模式从被动应对跨入主动预防时代。”
——现场生产总监 李振华
杉维矿石粒度检测方案核心优势
- 工业级可靠性:IP68防护等级,-30℃~70℃宽温运行,适应矿山高粉尘环境;
- 精准算法模型:30万+矿石样本训练的AI识别引擎,自适应不同岩性、光照条件;
- 快速部署:模块化设计,72小时内完成安装调试,兼容主流PLC/MES系统。