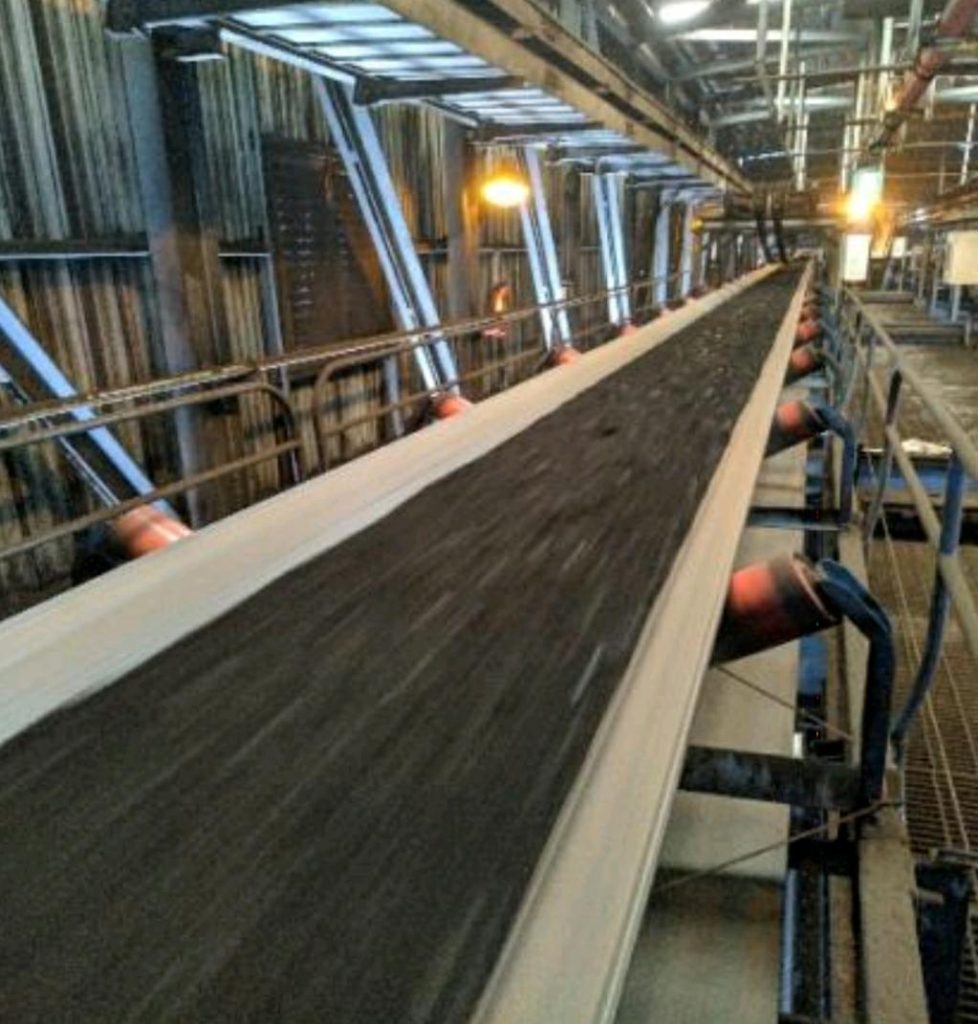
项目背景:电力巨头的燃煤管理挑战
印尼国家电力公司(PLN)作为东南亚最大的电力供应商之一,其位于廖内省的PLTU Tenayan燃煤电厂承担着区域电力供应的重要任务。电厂每日需通过04号皮带输送机将数千吨煤炭从堆场运输至锅炉仓,但传统人工采样和静态计量方式存在显著痛点:
- 数据滞后:人工测量无法实时反馈煤炭流量,导致燃料调度与发电计划脱节;
- 精度不足:煤炭密度波动导致体积-质量换算误差高达15%,影响成本核算;
- 安全隐患:人工频繁接近运行中的输送机,增加作业风险。
为突破瓶颈,PLN联合技术团队启动**“LiDAR实时监测系统”项目**,目标通过3D工业视觉技术实现煤炭运输全流程数字化管控。
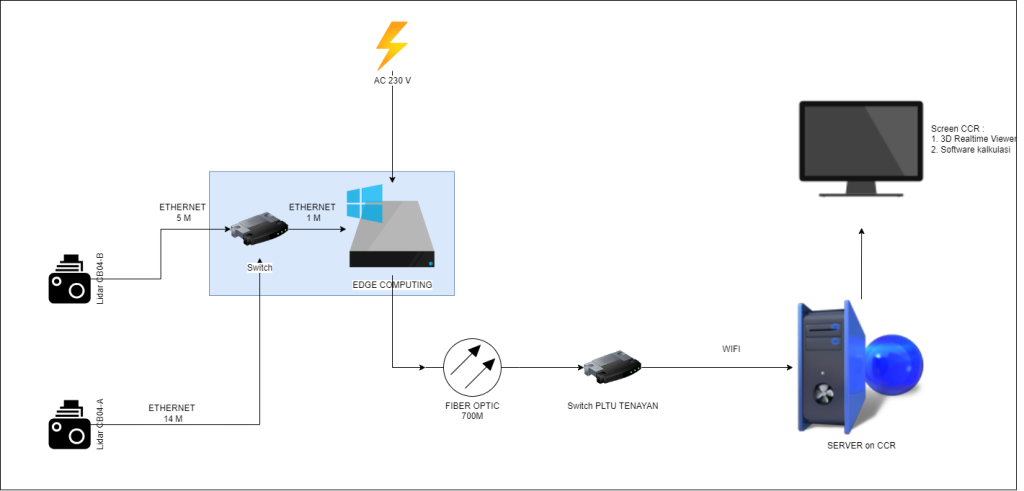
技术方案:杉维LiDAR+边缘计算架构
项目采用工业级LiDAR为核心传感器,搭配定制化边缘计算平台,构建端到端智能监测系统:
1. 硬件部署:精准适配严苛工业环境
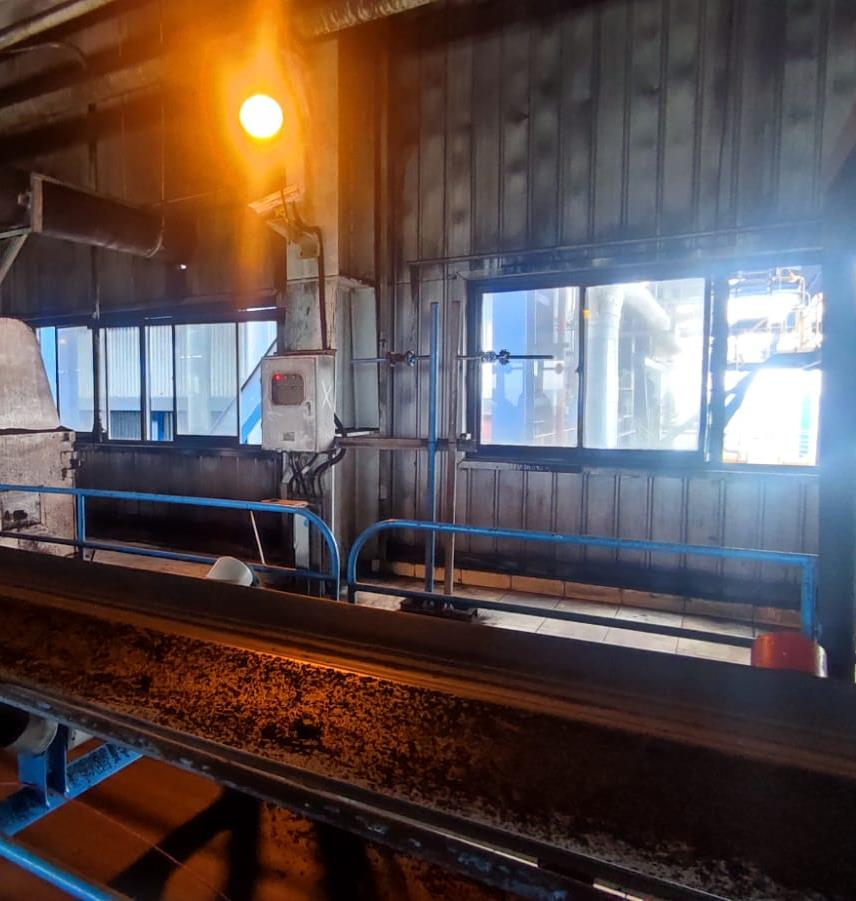
LiDAR选型:
270°水平视场角覆盖输送机全宽,40米检测距离适应高速传输场景;
IP65防护等级与-25°C~+60°C温宽,保障粉尘、高温环境稳定运行;
45kHz采样率+0.25°角分辨率,单次扫描捕获超20万点云数据。
安装设计:
双LiDAR单元(04A/04B)部署于输送机关键节点(距皮带中心线2.55米,高3.65米),消除测量盲区;
模块化可拆卸支架,支持快速安装与维护,避免产线停工。
2. 算法引擎:从点云到业务数据的智能转化
- 动态基准建模:
- LiDAR先扫描空载皮带生成基准3D模型(V_empty);
- 实时扫描载煤皮带点云数据(V_lidar),通过差值计算煤炭体积(V_material = V_lidar – V_empty)。
- 多参数融合计算:
- 结合皮带速度、煤炭密度历史数据,动态输出质量流量(t/h)、累计运量(t)及堆积密度(kg/m³);
- AI算法自动过滤输送机振动、粉尘干扰,精度提升至98.5%。
3. 系统集成:数据驱动决策闭环
- 边缘计算节点:
- 现场部署工业级服务器,实时处理TB级点云数据,延迟<500ms;
- 支持UDP/USB多协议输出,无缝对接电厂DCS系统。
- 中央控制室(CCR)可视化:
- 双屏监控:3D实时煤流模型+趋势分析仪表盘;
- 异常预警:堵料、偏载等工况触发声光报警,响应时间<2秒。

实施亮点:从设计到落地的标准化攻坚
1. 布线工程:零停机改造
- 光纤骨干网:
- 铺设700米抗干扰单模光纤,连接边缘节点与中央控制室;
- 采用“随工验收”模式,利用电厂检修窗口完成穿线,避免影响生产。
- POE供电优化:
- LiDAR与边缘设备通过以太网供电(PoE),减少独立电源布线复杂度;
- 冗余设计保障99.99%供电可靠性。
2. 协同验证:产学研深度合作
- 联合印尼理工大学(ITS)开展3阶段校准测试:
- 实验室标定:模拟不同煤种、湿度条件下的数据一致性;
- 空载验证:连续72小时监测空皮带,确认系统稳定性;
- 负载比对:与地磅称重数据交叉校验,误差率<1.2%。
成果效益:数字化赋能的三大跃升
维度 | 传统模式 | LiDAR系统 | 提升效果 |
---|---|---|---|
数据时效 | 人工记录,延迟4-6小时 | 实时更新,延迟<1秒 | 调度决策效率提升300% |
计量成本 | 年人工成本约12万美元 | 硬件维护费<3万美元/年 | 运营成本降低75% |
安全风险 | 每月2-3次高危靠近作业 | 全程无人值守 | 工伤事故归零 |
客户证言
“LiDAR系统上线后,燃料库存偏差从8%降至0.5%,年度因燃煤计量误差导致的损失减少约180万美元。更重要的是,它让我们首次实现了发电计划与燃料供应的动态平衡。”
——PLN Tenayan电厂运营总监
核心价值标签:#实时计量 #零接触巡检 #成本精益化 #工业4.0