项目背景
客户是一家水泥厂商,目前在熟料装车工序配备了6条胶带输送机,每天每条皮带的出货量可达13300吨。在熟料装车环节,该企业长期依赖人工操作,经验丰富的员工需要手动控制下料过程。然而,这种传统方式存在诸多问题,不仅影响生产效率,还导致管理上的难题。
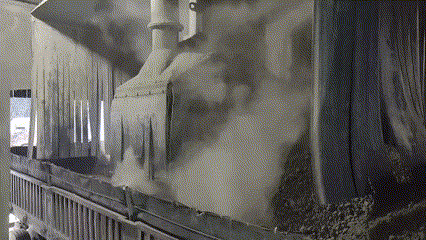
- 材料溢出问题:人工下料易受人为因素影响,稍有不慎便会导致材料溢出,造成资源浪费和现场污染。
- 人力浪费:淡季时出货量减少,但仍需安排人员值守,增加了不必要的人工成本。
- 管理难度高:旺季时需24小时连续装料,必须安排2-3人轮班,且需从其他岗位临时调配人手,管理难度大。
杉维卡车体积测量系统
为了帮助客户提升装车效率并优化人力成本,杉维科技团队对现场进行了全面调研,并推出了一套基于卡车车牌识别系统的卡车体积测量系统。该方案结合激光雷达、车牌识别系统和智能摄像头,可实现对卡车体积的精准测量,并结合编码器实时定位下料口,实现智能精准下料。
方案实施原理
杉维卡车体积测量系统是一套自主研发的基于激光雷达的智能测量系统。其核心工作流程如下:
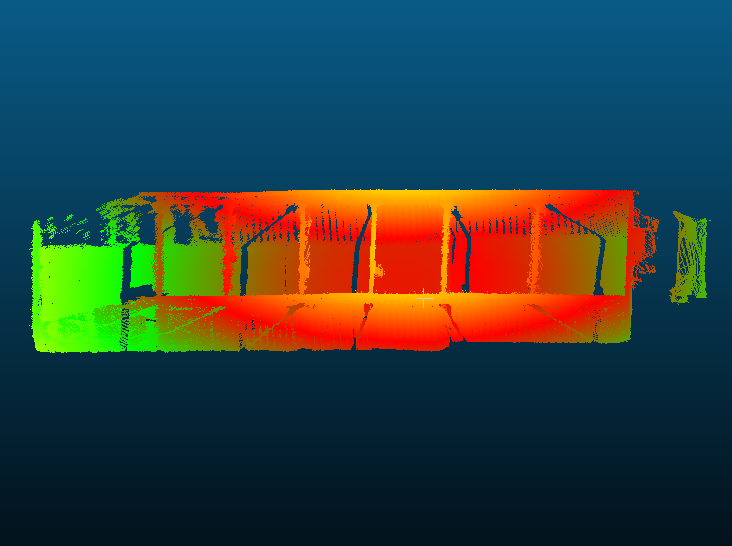
- 车牌识别:当卡车进入测量区域,车牌识别系统自动录入车辆信息,并触发体积测量系统。
- 自动测量:测量系统通过高分辨率混合固态式激光雷达扫描车斗,获取长、宽、高及容积数据。
- 智能计算与装料:后台AI算法计算出最优装料量,并将数据传输至下料系统,确保装料精准。
- 自动装料:卡车进入装料区域后,系统根据测量数据进行精准下料,无需人工干预。
卡车体积测量系统优化与改进
在项目实施过程中,杉维科技团队针对客户现场存在的问题,进行了针对性优化:
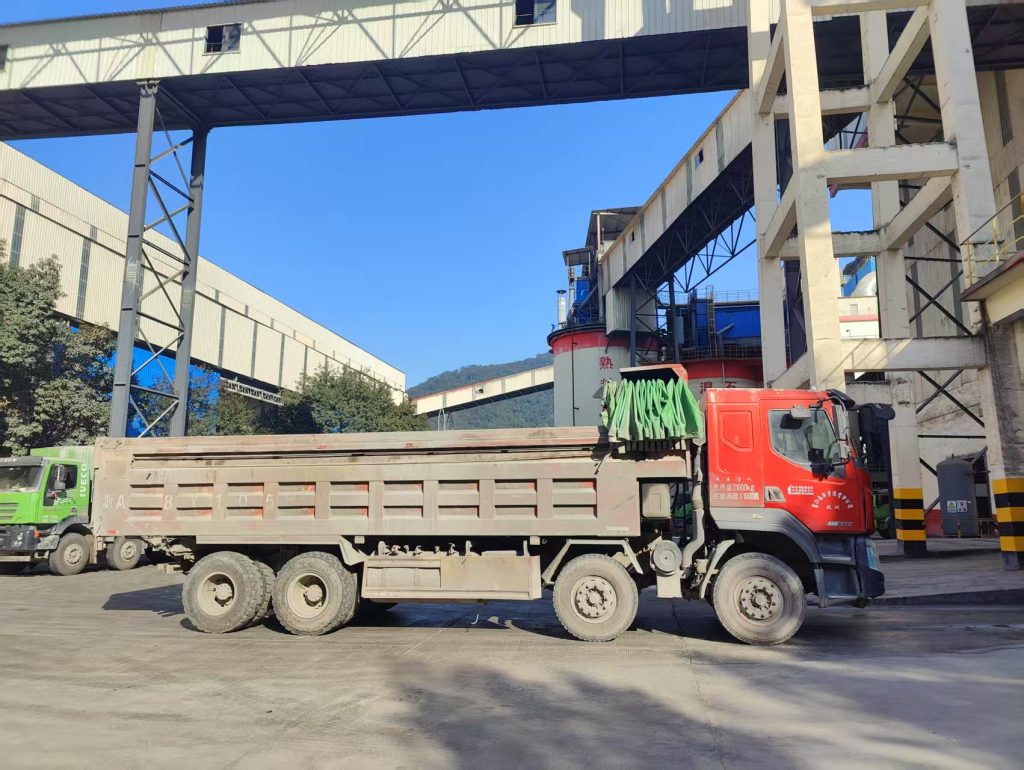
1. 车篷识别功能,避免测量失败
- 由于部分车辆装有帆布遮盖,司机可能会忘记打开车篷,导致测量失败。
- 改进方案:系统软件增加车篷识别功能,如发现车篷未打开,系统会自动提示司机操作,确保测量准确。
2. 可调节装料量,提升运输安全性
- 部分卡车需要长途运输,高速行驶时,装料过满可能导致材料飞溅,影响行车安全。
- 改进方案:系统增加装料重量自定义设置,司机可根据运输需求调整装料量,确保运输安全。
卡车体积测量项目成果与客户收益
杉维科技的智能化装料系统成功部署后,客户获得了显著的业务提升:
- 无人值守,实现自动化装料
- 司机自行完成装料,无需专人值守。
- 省去了一名固定岗位人员,大幅降低人工成本。
- 运营更加灵活,无需因季节性波动调整人手。
- 信息可追溯,优化生产管理
- 所有出货信息可通过后台系统查询,提升透明度。
- 便于生产备料管理,实现更加科学的生产规划。
- 减少浪费,提高装料精准度
- 通过精准测量与智能装料,杜绝材料溢出。
- 避免超载或装料不足,提高运输安全性。
总结
杉维科技的智能装料系统成功帮助客户优化人力配置、提高生产效率、降低运营成本。通过智能化手段,该水泥厂商实现了从传统手动装料到智能自动化装料的转型,为未来的数字化升级奠定了基础。
如果您的企业也面临类似的装料管理难题,欢迎联系我们,探索更加智能高效的解决方案!